In modernen industriellen Produktionsprozessen sind viele Fertigungs- und Montageschritte bereits automatisiert. Dennoch gibt es zahlreiche Tätigkeiten, die weiterhin von Hand ausgeführt werden müssen. Besonders in Bereichen, in denen monotone Abläufe eine hohe Konzentration erfordern, besteht trotz größter Sorgfalt die Möglichkeit menschlicher Fehler. Um solche Fehler frühzeitig zu erkennen und zu korrigieren, bevor sie sich im weiteren Produktionsverlauf auswirken, kommen zunehmend automatisierte Prüfsysteme zum Einsatz.
Ein besonders effektives Verfahren ist die bildgestützte Qualitätskontrolle. Hierbei erfassen Kameras den Zustand eines Bauteils direkt nach einem Montageschritt. Mithilfe eines auf Anomalieerkennung spezialisierten Algorithmus wird geprüft, ob alle erforderlichen Teile korrekt verbaut sind. Ist dies der Fall, kann der Prozess automatisch fortgesetzt werden. Wird jedoch eine Abweichung erkannt, erhält der Mitarbeiter gezielte Hinweise zur Korrektur.
Das Fraunhofer-Institut für Optronik, Systemtechnik und Bildauswertung (IOSB) in Karlsruhe hat ein solches Prüfsystem gemeinsam mit der Dr. Ing. h.c. F. Porsche AG entwickelt und an einem konkreten Beispiel aus der Getriebefertigung umgesetzt.
Praxisbeispiel: Getriebekomponenten-Montage
In diesem Szenario arbeitet ein Mitarbeiter an einer Station, an der ihm auf einem Drehteller zwei Hälften eines Getriebes präsentiert werden. Seine Aufgabe besteht darin, bestimmte Bauteile präzise einzusetzen: In eine Hälfte müssen eine Einstellscheibe sowie eine Flächendichtung eingebracht werden, in der anderen sind 18 Schrauben korrekt in vorbereitete Bohrungen einzusetzen. Zwei der Bohrungen müssen jedoch zwingend freibleiben, da sie für die Greifvorrichtung eines nachfolgenden Roboters bestimmt sind. Fehlerquellen sind daher unter anderem fehlende Bauteile oder Schrauben in nicht vorgesehenen Bohrungen.
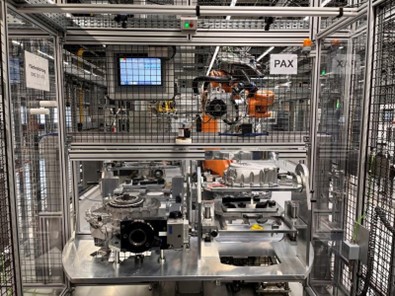
Ziel der gemeinsam entwickelten Lösung war es, solche Fehler zuverlässig zu erkennen, ohne den Produktionsfluss unnötig zu verlangsamen. Das Prüfsystem wird aktiv, sobald der Mitarbeiter seine Aufgabe abgeschlossen und per SPS-Steuerung den nächsten Schritt – die Übergabe an den Roboter – ausgelöst hat. Zwei Kameras nehmen jeweils ein senkrechtes Bild der Getriebehälften auf. Diese Aufnahmen werden anschließend von einem KI-gestützten Modell analysiert, das prüft, ob alle Komponenten korrekt platziert wurden.
Maschinelles Lernen mit Patchcore
Die Grundlage des Systems bildet ein Machine-Learning-Verfahren namens Patchcore, das für die sogenannte Ein-Klassen-Klassifikation eingesetzt wird. Dabei wird das System ausschließlich mit Bildern von korrekt bestückten Bauteilen trainiert – also dem angestrebten Soll-Zustand. Anhand dieser Daten lernt das Modell, wie ein fehlerfreier Aufbau aussieht. Der große Vorteil dieser Methode liegt darin, dass in der Realität vor allem fehlerfreie Montagezustände auftreten, sodass ausreichend Trainingsmaterial verfügbar ist. Fehlerhafte Beispiele sind dagegen selten und aufwendig zu erzeugen.
Während des Betriebs generiert das Patchcore-Modell zu jedem Bild einen sogenannten Anomalie-Score sowie eine visuelle Darstellung (Heatmap), in der potenzielle Fehlerstellen markiert werden. Wie bei jeder Klassifikation besteht auch hier das Risiko von Fehlentscheidungen – entweder durch Übersehen eines Fehlers (false negative oder „Pseudo i.O.“) oder durch fälschliche Kennzeichnung einer korrekten Montage als fehlerhaft (false positive oder „Pseudo N.i.O.“).
Letzteres bedeutet, dass ein Mitarbeiter unnötigerweise eine korrekte Ausführung überprüfen muss, was Zeit kostet. Ersteres hingegen kann dazu führen, dass ein defektes Bauteil weiterverarbeitet wird – was es in jedem Fall zu vermeiden gilt.
Testphase in der Serienfertigung
Zur Evaluierung wurde das System in eine laufende Produktionslinie bei Porsche eingebunden. Jeweils über den beiden Getriebehälften wurde eine Kamera installiert. Nachdem der Mitarbeiter seine Aufgabe abgeschlossen und den Startknopf zur Übergabe betätigt hatte, erfassten die Kameras die Situation, ohne das aktuelle Produktionsgeschehen zu beeinflussen. Während der zweiwöchigen Testphase war das System im Hintergrund aktiv, gab aber noch keine Rückmeldung an die Mitarbeiter.
Das Ziel war, eine Pseudo-N.i.O.-Rate von maximal einem Prozent zu erreichen – eine Vorgabe von Porsche, um unnötige Unterbrechungen der Produktionslinie zu vermeiden und die Akzeptanz bei den Mitarbeitenden zu sichern.
Die Ergebnisse fielen äußerst positiv aus: Bei der Analyse von rund 1.000 Bildpaaren pro Getriebehälfte wurde kein einziger „Pseudo i.O.“-Fall festgestellt – also keine nicht erkannte Anomalie. Zwei tatsächliche Fehler wurden korrekt identifiziert: einmal fehlte eine Schraube, einmal war eine Schraube in einer unzulässigen Bohrung platziert. Die Pseudo-N.i.O.-Rate lag bei lediglich 0,2 Prozent – deutlich unter dem geforderten Schwellenwert.
Fazit
Mit der erfolgreichen Integration und Erprobung des bildbasierten Prüfsystems in der Getriebefertigung konnte das Fraunhofer IOSB zeigen, dass moderne KI-Verfahren zur Anomalieerkennung nicht nur zuverlässig arbeiten, sondern auch praktikabel in bestehende Produktionsprozesse integriert werden können. Die niedrige Fehlerquote und die schnelle Reaktionsmöglichkeit machen solche Systeme zu wertvollen Werkzeugen in der Qualitätssicherung – besonders in Prozessen, in denen menschliche Aufmerksamkeit trotz hoher Präzision an ihre Grenzen stößt.